Deal with change
Identify risks that affect your business so that you grow and sustain your business.
QualWerx helps small to medium sized businesses identify and deal with the hurdles to success
- Identify and mitigate risk
- Manage your business according to success factors
- Minimize exposure to mischance or error
- Prevent damage to or loss of product
- Growth opportunities and timelines
Sometimes, what is needed is a document which explains how things are made.
QualWerx helps small to medium sized manufacturers successfully register to quality standards, including
- ISO 9001:2015
- ISO 13485:2016
- AS9100D
- ISO 14001:2015
- TS29001
Our Specialties
Need an objective eye and experienced help? Get In Touch For a Free ConsultationMANAGEMENT CONSULTING
It is a broad subject. It is usually late-for-impact and overpriced if it is tied to a big formal project. It is timely and often actionable when it is given informally on a few well-focused topics. It is all about managing risk to success. It is advice from an objective observer who has gained wisdom from multiple real-time observations and learned from other’s mistakes who desires to apply that wise experience to your situation.
ROOT CAUSE ANALYSIS & TRAINING
RCA is a useful technique to help teams learn from their mistakes. If neglected, it will mean mistakes can only get more frequent and costly. A Root Cause is the beginning point or ‘Genesis’ event that triggers actions which result in a particular affect. A well stated root cause defines why something went wrong or right. If it is time to learn from mistakes and if your team is ready to focus on processes rather than assign blame, it can become a practical part of changing your corporate culture.
QUALITY TRAINING
This is an eclectic and broad subject that often has negative baggage associated with it. Why not get small doses of interesting and practical skills instead? The topics could range from the importance of timeliness, to data analysis methods, to defining your organizational bottlenecks, to the key AS9100 requirements that affect your purchasing process, to the most practical method to define your MDR.
INTERNAL AUDITING
No, this is not the same as a colonoscopy. Learn the methods to become a helpful process sleuth, and simultaneously avoid becoming a legend in your own mind. Internal auditing is much more about learning and verifying something as fact as you talk with a process expert than it is about completing a ten-page checklist. You will also learn that the onus for a good internal audit is all about your attitude and your preparation.
PROCESS FLOW CHARTING AND DOCUMENTING
Sometimes, it is really valuable to have a picture and words that describe how things get combined and massaged to create something new. Lets call that new thing “a Product.” Lets call the picture and descriptive words a “Recipe.” Clearly describing the “recipe” to make “product” is about art, logic and information. Building it is often very creative and is demanding to manage. There is no one “recipe” (Flowcharting method) that QualWerx will recommend. That is because what is most valuable is determined by the recipient/user who will actually use the ‘Process Recipe’ to ensure that something valuable and reliable (your “product”) is delivered on-time to your customer.
SUCCESSFUL REGISTRATION TO QUALITY STANDARDS
Let QualWerx apply the experience of getting companies registered and keeping them registered to a “Standard” according to the demands of your most valuable customers. Registration to a standard coupled with managing processes and profits by fact can truly improve and sustain your business. Do not pursue Registration without business commitments from your customers.
SUPPLIER AUDITING
This activity is similar to internal auditing, but, is only useful when the practitioner is able to be schizophrenic. This means, the practitioner keeps one eye on the true end customer and one eye on requirements and the other eye on value. It requires the attitude that rather than trying to win, the practitioner should ‘get-out-of-the-box’ and actually work with the supplier to assist them to become more profitable and reliable.
QUALITY SYSTEM MAINTENANCE AND SYSTEM AUDITING
This is a combination of all of the above services. It is the management of all the above-mentioned services and the coaching to make “Plan-Do-Check-Act” your usual approach and mind-set.
COST OF POOR QUALITY (COPQ)
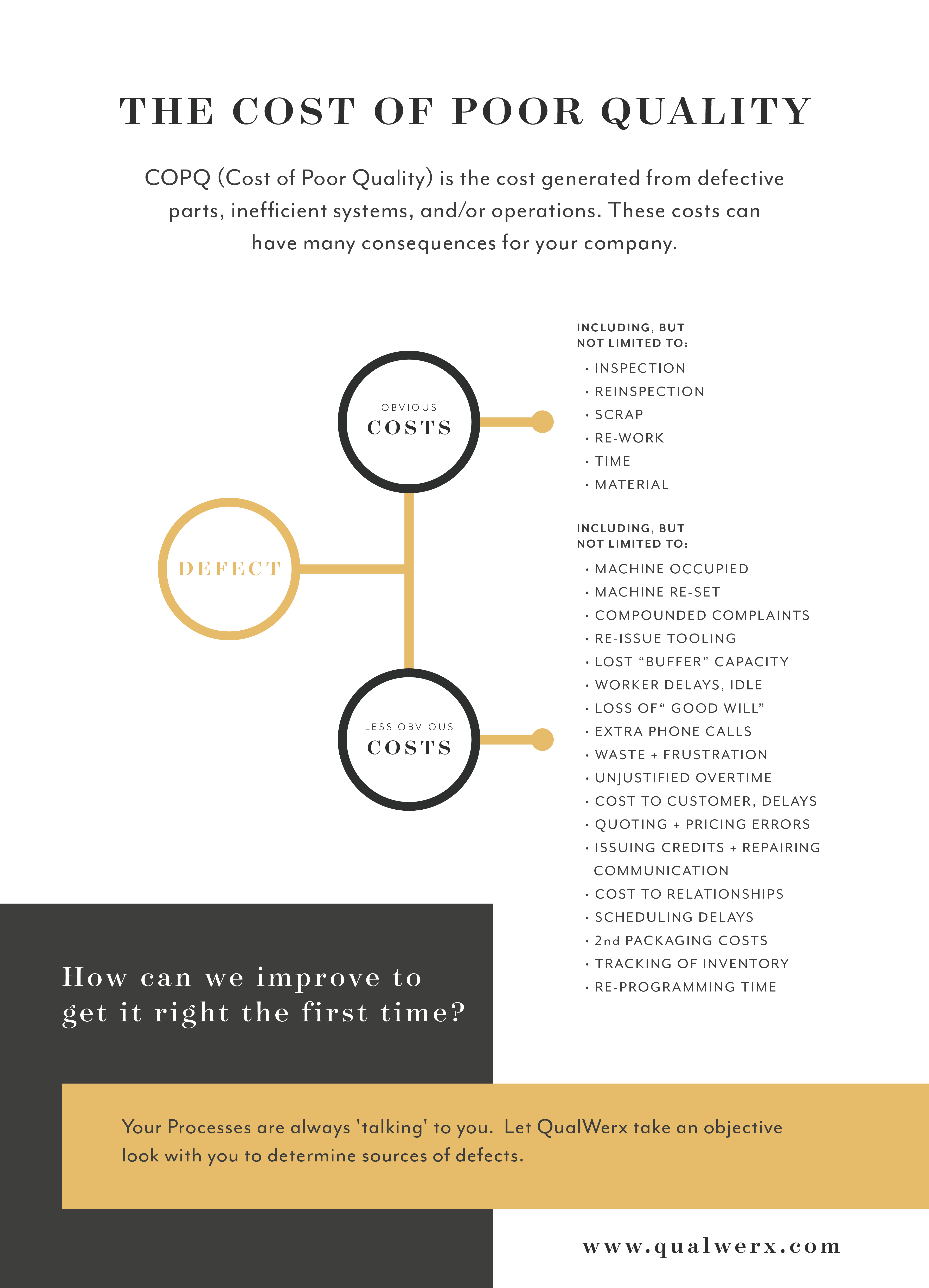
Services
What We Can Do For You
Become better prepared for ventures and opportunities that carry risk of failure. Develop methods to identify and deal with risks to success. Acquire and build a new mindset to better consider positive and negative factors for success.
Define the current reality
define what is
Define the new, desired outcome
define where you want to be
Find the gaps or disconnects between reality and desired outcome
define gaps between the “is” and the “want to be” positions
Work with the client to fill the gaps
plan and follow through the steps to get where you need to be
From Our Founder
We Can Help
Risks are everywhere. Spotting them, prioritizing them and dealing with them while sustaining your current operations
and activities is half the battle for success. The other half is predicting the next big risk to your success. Keeping an objective viewpoint on these challenges is invaluable to the identification, assessment, as well as
prediction of operational hazards and risks.
The types of companies in which I have consulted and successfully implemented risk mitigation methods include sheet metal fabricators, machining / manufacturing shops, plating and anodizing providers, heat treat providers, investment casting manufacturers, small foundries, and
product or materials distributors.
and activities is half the battle for success. The other half is predicting the next big risk to your success. Keeping an objective viewpoint on these challenges is invaluable to the identification, assessment, as well as
prediction of operational hazards and risks.
The types of companies in which I have consulted and successfully implemented risk mitigation methods include sheet metal fabricators, machining / manufacturing shops, plating and anodizing providers, heat treat providers, investment casting manufacturers, small foundries, and
product or materials distributors.